LM5085EVAL/NOPB National Semiconductor, LM5085EVAL/NOPB Datasheet - Page 2
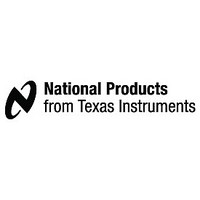
LM5085EVAL/NOPB
Manufacturer Part Number
LM5085EVAL/NOPB
Description
EVAL BOARD FOR LM5085
Manufacturer
National Semiconductor
Datasheet
1.LM5085EVAL.pdf
(14 pages)
Specifications of LM5085EVAL/NOPB
Lead Free Status / RoHS Status
Lead free / RoHS Compliant
www.national.com
Refer to the LM5085 data sheet for a detailed block diagram,
and a complete description of the various functional blocks.
Board Layout and Probing
The pictorial in Figure 1 shows the placement of the circuit
components. The following should be kept in mind when the
board is powered:
1) When operating at high input voltage and continuous con-
duction mode forced air flow is necessary to prevent over-
heating of the LM5085 controller.
2) When operating at high load current forced air flow may be
necessary to prevent overheating of Q1, D1, and L1. These
components may be hot to the touch.
3) Use CAUTION when probing the circuit at high input volt-
ages to prevent injury, as well as possible damage to the
circuit.
4) At maximum load current (4.5A), the wire size and length
used to connect the source voltage, and the load, becomes
important. Ensure there is not a significant drop in the wires
supplying the input current and the load current.
Board Connection/Start-up
The input connections are made to the J1 (+) and J2 (-) con-
nectors. The load is connected to the J3 (VOUT) and J4
(GND) terminals. Ensure the wires are adequately sized for
the intended load current. Before start-up a voltmeter should
be connected to the input terminals, and one to the output
terminals. The load current should be monitored with an am-
meter or a current probe. It is recommended that the input
voltage be increased gradually to 4.5V, at which time the out-
put voltage should be slightly less than 4.5V, depending on
the load current. The output is regulated at 5V when the input
voltage is increased above 5V. If the output voltage is correct,
then increase the input voltage as desired and proceed with
evaluating the circuit. DO NOT EXCEED 60V AT VIN. Ex-
ceeding 60V can result in damage to Q1 and/or D1.
Load Current Derating
Although the maximum load current for this evaluation board
is specified as 4.5A, the data sheet for the Si7465 PFET
specifies a maximum continuous current of 3.2A. Since the
input current, which is the average current though Q1, in-
creases as the input voltage is decreased, the load current
must be derated at low input voltage. Please refer to the graph
“Maximum Load Current Derating” below.
FIGURE 2. Maximum Load Current Derating
30072003
2
Operating at Low Voltage
When the input voltage is less than 5V the PFET (Q1) is on
continuously (100% duty cycle), and the output voltage is
equal to the input voltage, minus voltage drops across the
sense resistor, Q1 and the inductor. As the input voltage is
increased above 5V switching commences at the PGATE pin
and the SW node as the LM5085 regulates the output at 5V.
Since the LM5085 does not have a required minimum off-
time, the circuit transitions smoothly from 100% duty cycle to
a regulated output.
Current Limit
The LM5085 peak current limit detection operates by sensing
the voltage across either the R
(R5), during the on-time and comparing it to the voltage
across R3 at the ADJ pin. The current limit threshold is
reached when the sensed voltage exceeds the voltage across
R3. When current limit is reached Q1 is immediately switched
off. The current limit function is much more accurate and sta-
ble over temperature when a sense resistor is used. The R
(ON)
temperature coefficient.
Current sensing is disabled for a blanking time of
the beginning of each on-time to prevent false triggering of
the current limit comparator due to leading edge current
spikes. After Q1 is turned off due to current limit detection, Q1
is held off for a longer-than-normal off-time. The extended off-
time is a function of the input voltage and the voltage at the
FB pin, as shown below in the graph “Current Limit Off-time
vs. V
from the following:
The longer-than-normal forced off-time allows the inductor
current to decrease to a low level before the next on-time. This
cycle-by-cycle monitoring, followed by a long forced off-time,
provides effective protection from output load faults over a
wide range of operating conditions.
of a MOSFET has a wide process variation and a large
FIGURE 3. Current Limit Off-time vs. V
IN
and V
FB
”. The current limit off-time can be calculated
DS(ON)
of Q1, or a sense resistor
IN
30072005
and V
≊
100 ns at
FB
DS