NCN8024DWR2G ON Semiconductor, NCN8024DWR2G Datasheet - Page 11
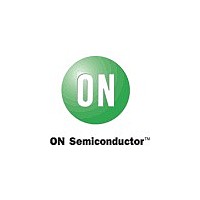
NCN8024DWR2G
Manufacturer Part Number
NCN8024DWR2G
Description
IC SMART CARD IC2 8SOIC
Manufacturer
ON Semiconductor
Datasheet
1.NCN8024DTBR2G.pdf
(16 pages)
Specifications of NCN8024DWR2G
Applications
Smart Card Reader, Writer
Voltage - Supply
5V
Package / Case
28-SOIC (0.300", 7.50mm Width)
Mounting Type
Surface Mount
Lead Free Status / RoHS Status
Lead free / RoHS Compliant
Interface
-
Available stocks
Company
Part Number
Manufacturer
Quantity
Price
according to the below relationship considering an external
resistor divider R1 / R2 (see block diagram Figure 1):
threshold (V
can be interesting to adjust this threshold at a higher value
and by the way increase the V
level which enables a deactivation sequence if the V
voltage is too low.
minimum supply voltage insuring a correct operating is
higher than 2.55 V, increasing UVLO
consequently necessary. Considering for instance a resistor
bridge with R1 = 56 kW, R2 = 42 kW and V
typical the V
than 2 V.
CLOCK DIVIDER:
depending upon the specific application, prior to be applied
to the smart card driver. These division ratios are
programmed using pins CLKDIV1 and CLKDIV2 (see
Table 1). The input clock is provided externally to pin
CLKIN.
maximum frequency signal (considering a division ratio w
2). Of course, the ratio must be defined by the user to cope
with Smart Card considered in a given application
range specification, the divider is synchronized by the last
flip flop, thus yielding a constant 50% duty cycle, whatever
be the divider ratio 1/2, 1/4 or 1/8. On the other hand, the
output signal Duty Cycle cannot be guaranteed 50% if the
division ratio is 1 and if the input Duty Cycle signal is not
within the 46 − 56% range at the CLKIN input.
external controller, the clock will be applied to the card
under the control of the microcontroller or similar device
after the activation sequence has been completed.
Table 1. Clock Frequency Programming
PORADJ pin is used to modify the UVLO threshold
If PORADJ is connected to Ground the V
For example, there are microcontrollers for which the
The minimum dropout detection voltage should be higher
The maximum detection level may be up to VDD.
The input clock can be divided by 1/1, 1/2, 1/4, or 1/8,
The clock input stage (CLKIN) can handle a 27 MHz
In order to avoid any duty cycle out of the 45% / 55%
When the signal applied to CLKIN is coming from the
CLKDIV1
0
0
1
1
UVLO + 59k ) 42k
DD
DD
dropout detection level can be increased up to:
falling) is typically 2.35 V. In some cases it
UVLO + R1 ) R2
42k
CLKDIV2
0
1
0
1
R2
DD
V
POR −
supply dropout detection
V
POR
VDD
+ 2.75 V
(V
CKLKIN / 4
POR−
F
CLKIN / 2
CLKIN/8
DD
CRD_CLK
CLKIN
DD
falling) is
= 1.18 V
UVLO
http://onsemi.com
DD
11
DATA I/O, AUX1 and AUX2 LEVEL SHIFTERS
AUX2 adapt the voltage difference that might exist between
the micro−controller and the smart card. These three
channels are identical. The first side of the bidirectional
level shifter dropping Low (falling edge) becomes the driver
side until the level shifter enters again in the idle state pulling
High CRD_IO and I/Ouc.
integrated on each terminal of the bidirectional channel. In
addition with these pull−up resistors, an active pull−up
circuit provides a fast charge of the stray capacitance.
internally to 15 mA and the maximum frequency on these
lines is 1 MHz.
STANDBY MODE
mode. A minimum number of circuits are active while
waiting for the microcontroller to start a session:
•
•
•
•
•
POWER−UP
presence of a card using the signals INT and CMDVCC as
shown in Table 2:
active) the controller can start a card session by pulling
CMDVCC Low. Card activation is run (t0, Figure 5). This
Power−Up Sequence makes sure all the card related signals
are LOW during the CRD_V
lines are validated when CRD_V
minimum voltage specified. When the CRD_V
reaches the programmed value (3.0 V or 5.0 V), the circuit
activates the card signals according to the following
sequence (Figure 5):
•
•
•
•
Table 2. Card Presence State
The three bidirectional level shifters I/O, AUX1 and
Passive 11 kW pull−up resistors have been internally
The current to and from the card I/O lines is limited
After a Power−on reset, the circuit enters the standby
In the standby mode the microcontroller can check the
If a card is detected present (CRD_PRES or CRD_PRES
All card contacts are inactive
Pins I/Ouc, AUX1uc and AUX2uc are in the
high−impedance state (11 kW pull−up resistor to V
Card pins are inactive and pulled Low
Supply Voltage monitoring is active
The internal DC/DC converter oscillator is running.
CRD_V
I/O, AUX1 and AUX2 lines are activated (t2)
Then Clock channel is activated and the clock signal is
applied to the card (t3)
Finally the Reset level shifter is enabled (t4)
HIGH
LOW
INT
CC
is powered−up at its nominal value (t1)
CMDVCC
HIGH
HIGH
CC
positive going slope. These
CC
is stable and above the
Card not present
Card present
State
CC
voltage
DD
)