OKX2-T/10-D12P-C Murata Power Solutions Inc, OKX2-T/10-D12P-C Datasheet - Page 8
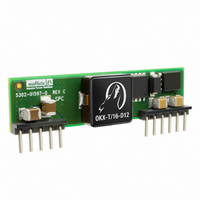
OKX2-T/10-D12P-C
Manufacturer Part Number
OKX2-T/10-D12P-C
Description
CONVERT DC/DC SIP 50W 0.75-5.5V
Manufacturer
Murata Power Solutions Inc
Series
Okami™ OKX-T/10-D12r
Type
Point of Load (POL) Non-Isolatedr
Specifications of OKX2-T/10-D12P-C
Number Of Outputs
1
Output
0.75 ~ 5.5V
Power (watts)
50W
Mounting Type
Through Hole
Voltage - Input
8.3 ~ 14V
Package / Case
11-SIP Module
1st Output
0.75 ~ 5.5 VDC @ 10A
Size / Dimension
2.00" L x 0.37" W x 0.50" H (50.8mm x 9.4mm x 12.7mm)
Power (watts) - Rated
50W
Efficiency
94.5%
Approvals
cUL, EN, UL
Output Power
55 W
Input Voltage Range
8.3 V to 14 V
Output Voltage (channel 1)
0.7525 V to 5.5 V
Output Current (channel 1)
10 A
Output Voltage (channel 2)
0.7525 V to 5.5 V
Output Current (channel 2)
10 A
Output Voltage (channel 3)
0.7525 V to 5.5 V
Output Current (channel 3)
10 A
Package / Case Size
SIP
Output Voltage
0.7525 V to 5.5 V
Product
Non-Isolated / POL
Dc / Dc Converter O/p Type
Adjustable
No. Of Outputs
1
Input Voltage
8.3V To 14V
Power Rating
50W
Output Current
10A
Approval Bodies
EN / FCC / IEC / UL
Rohs Compliant
Yes
Lead Free Status / RoHS Status
Lead free / RoHS Compliant
Operating Temperature
-
3rd Output
-
2nd Output
-
Lead Free Status / Rohs Status
Lead free / RoHS Compliant
Other names
811-2014-5
Available stocks
Company
Part Number
Manufacturer
Quantity
Price
Part Number:
OKX2-T/10-D12P-C
Manufacturer:
MURATA/村田
Quantity:
20 000
impedances between the power supply and its load. In order to minimize circuit
errors and standardize tests between units, scope measurements should be
made using BNC connectors or the probe ground should not exceed one half
inch and soldered directly to the fi xture.
All models regulate within specifi cation and are stable under no load to full
load conditions. Operation under no load might however slightly increase
output ripple and noise.
To prevent many over temperature problems and damage, these converters
include thermal shutdown circuitry. If environmental conditions cause the
temperature of the DC/DC’s to rise above the Operating Temperature Range
up to the shutdown temperature, an on-board electronic temperature sensor
will power down the unit. When the temperature decreases below the turn-on
threshold, the converter will automatically restart. There is a small amount of
temperature hysteresis to prevent rapid on/off cycling. The temperature sensor
is typically located adjacent to the switching controller, approximately in the
center of the unit. See the Performance and Functional Specifi cations.
shut down suddenly without warning. Be sure to thoroughly test your applica-
tion to avoid unplanned thermal shutdown.
The graphs in the next section illustrate typical operation under a variety of
conditions. The Derating curves show the maximum continuous ambient air
temperature and decreasing maximum output current which is acceptable
under increasing forced airfl ow measured in Linear Feet per Minute (“LFM”).
Note that these are AVERAGE measurements. The converter will accept brief
increases in current or reduced airfl ow as long as the average is not exceeded.
itself which is obviously running at higher temperature than the outside air.
Also note that “natural convection” is defi ned as very fl ow rates which are not
using fan-forced airfl ow. Depending on the application, “natural convection” is
usually about 30-65 LFM but is not equal to still air (0 LFM).
cycle wind tunnel with calibrated airfl ow. We use both thermocouples and an
infrared camera system to observe thermal performance.
the converter may have an unplanned Over Temperature shut down. Also, these
graphs are all collected at slightly above Sea Level altitude. Be sure to reduce
the derating for higher density altitude.
The converter is extensively protected against current, voltage and temperature
extremes. However your output application circuit may need additional protec-
tion. In the extremely unlikely event of output circuit failure, excessive voltage
could be applied to your circuit. Consider using an appropriate fuse in series
with the output.
In the fi gure, the two copper strips simulate real-world printed circuit
Note that the temperatures are of the ambient airfl ow, not the converter
Murata Power Solutions makes Characterization measurements in a closed
If you operate too close to the thermal limits, the converter may
If you routinely or accidentally exceed these Derating guidelines,
www.murata-ps.com
As soon as the output current increases to approximately 125% to 150% of
its maximum rated value, the DC/DC converter will enter a current-limiting
mode. The output voltage will decrease proportionally with increases in output
current, thereby maintaining a somewhat constant power output. This is also
commonly referred to as power limiting.
below the rated tolerance. See the Performance/Functional Specifi cations.
Note particularly that the output current may briefl y rise above its rated value
in normal operation as long as the average output power is not exceeded. This
enhances reliability and continued operation of your application. If the output
current is too high, the converter will enter the short circuit condition.
When a converter is in current-limit mode, the output voltage will drop as the
output current demand increases. If the output voltage drops too low (approxi-
mately 98% of nominal output voltage for most models), the PWM controller
will shut down. Following a time-out period, the PWM will restart, causing the
output voltage to begin ramping up to its appropriate value. If the short-circuit
condition persists, another shutdown cycle will initiate. This rapid on/off cycling
is called “hiccup mode”. The hiccup cycling reduces the average output cur-
rent, thereby preventing excessive internal temperatures and/or component
damage. A short circuit can be tolerated indefi nitely.
The Sense input is normally connected at the load for the respective Sense
polarity (+Sense to the +Vout load). Sense inputs compensate for voltage drops
along the output wiring such as moderate IR drops and the current carrying
capacity of PC board etch. This output drop (the difference between Sense and
Vout when measured at the converter) should not exceed 0.5V. Use heavier
connections if this drop is excessive. Sense inputs also improve the stability of
the converter and load system by optimizing the control loop phase margin.
nect the Sense to their respective Vout at the converter pins.
Ground. Any long, distributed wiring and/or signifi cant inductance introduced
into the Sense control loop can adversely affect overall system stability. If in
doubt, test your applications by observing the converter’s output transient
response during step loads. There should not be any appreciable ringing or
oscillation.
in any external fi lter elements. Do not exceed maximum power ratings. Exces-
sive voltage differences between Vout and Sense together with trim adjustment
of the output can cause the overvoltage protection circuit to activate and shut
down the output.
output current and the highest output voltage at the ouput pins. Therefore the
designer must insure:
Current limiting inception is defi ned as the point at which full power falls
If the Sense function is not used for remote regulation, the user should con-
Sense lines on the PCB should run adjacent to DC signals, preferably
You may also adjust the output trim slightly to compensate for voltage loss
Power derating of the converter is based on the combination of maximum
(Vout at pins) x (Iout) ≤ (Max. rated output power)
Adjustable DOSA 10/16-Amp SIP DC/DC Converters
Page 8 of 16