MIC184YM Micrel Inc, MIC184YM Datasheet - Page 15
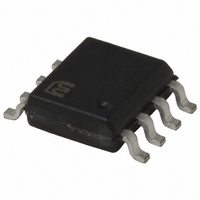
MIC184YM
Manufacturer Part Number
MIC184YM
Description
IC SUPERVISOR LOCAL/REMOTE 8SOIC
Manufacturer
Micrel Inc
Datasheet
1.MIC184YM.pdf
(20 pages)
Specifications of MIC184YM
Output Type
I²C™/SMBus™
Lead Free Status
Lead free
Function
Temp Monitoring System (Sensor)
Topology
ADC (Sigma Delta), Register Bank
Sensor Type
External & Internal
Sensing Temperature
-55°C ~ 125°C, External Sensor
Output Alarm
Yes
Output Fan
No
Voltage - Supply
2.7 V ~ 5.5 V
Operating Temperature
-55°C ~ 125°C
Mounting Type
Surface Mount
Package / Case
8-SOIC (3.9mm Width)
Temperature Sensor Function
Temp Sensor
Package Type
SOIC
Operating Temperature (min)
-55
Operating Temperature (max)
125C
Operating Temperature Classification
Military
Operating Supply Voltage (min)
2.7V
Operating Supply Voltage (typ)
3.3/5V
Operating Supply Voltage (max)
5.5V
Lead Free Status / RoHS Status
Compliant
Other names
576-1676-5
MIC184YM
MIC184YM
Available stocks
Company
Part Number
Manufacturer
Quantity
Price
Company:
Part Number:
MIC184YM
Manufacturer:
MICREL
Quantity:
263
Company:
Part Number:
MIC184YM TR
Manufacturer:
MICREL
Quantity:
2 500
Company:
Part Number:
MIC184YM-TR
Manufacturer:
RCA
Quantity:
6 221
Company:
Part Number:
MIC184YMM
Manufacturer:
FSC
Quantity:
764
Applications Information
Switching Zones
The recommended procedure for switching between the
internal and external zones is as follows:
At the conclusion of the serial bus transaction for step 4, the
A/D converter will begin a conversion cycle using the new
zone setting. The next conversion cycle completed after
the serial bus transaction for step 5 will result in the state of
the INT output being updated (if enabled) for the new zone.
Generally the MIC184’s A/D converter operates continuously,
but it will be halted and reset each time the part recognizes
its slave address on the serial bus. Interrupted conversions
will remain halted until the end of the host’s communication
with the MIC184. After the completion of step 5 and a delay
of t
for the new zone. The above routine is extremely unlikely
to miss a temperature event, as even one A/D conversion is
typically much slower than the I
control the MIC184. See Figure 6: A/D Converter Timing.
Step 2(c) is recommended because the MIC184 has only
one CONFIG register, corresponding to the active zone. In
order to preserve data integrity for both zones, 2(c) allows
the host to create a virtual CONFIG register for the inactive
zone by dedicating one byte of memory to that purpose.
Additional virtual registers may be created as needed by
inserting additional reads as steps 2(d), 2(e), etc. These
could for example correspond to the values in T_SET and
T_HYST immediately prior to switching zones. Steps 4(b) and
5 ensure that the MIC184 will enter the new zone searching
for an overtemperature event.
Identifying an MIC184 by Software Test
The MIC184 and the LM75 each have an eight-bit CON-
FIG register. In LM75-type parts, no more than seven of
May 2006
MIC184
CONV
1. Disable interrupts (if used)
2. Read the CONFIG register to:
3. Write the appropriate values to
4. Write to CONFIG as follows:
5. If interrupts are being used, MODE must then be
by setting the IM bit in CONFIG.
a) Verify no masked interrupt was pending
b) Clear STS prior to switching zones
c) Hold the settings of CONFIG register for the
T_SET and T_HYST for the new zone.
a) To toggle the ZONE bit (1 = remote, 0 =
b) If interrupts are being used, step 4 should
set to 1 and IM reset to 0
x Fault_Queue, STS and INT will contain the results
(D[7] = 0)
current zone
internal)
also clear MODE
2
C/SMBus transactions that
15
the eight bits of this register are used, and at least one bit
(the MSB) will always return a zero. The MIC184 uses all
eight bits of the CONFIG register: the MSB is the part’s
status bit (STS). A simple test by which the host can
determine whether a system has an MIC184 installed, or
is using a legacy LM75-type device, is to create a situation
which will set the MSB in the MIC184’s CONFIG register
and then determine if the MSB is in fact set. Two examples
of how this can be done are outlined below. The first is in-
terrupt-driven, the second uses software polling. Note that
both procedures generate one or more spurious interrupts.
The code for these tests should therefore temporarily dis-
able any affected interrupt routines.
{START Interrupt-Driven Test and Initialization
1. Disable the host’s overtemperature and under-
2. Write 0000 0010b (02h) to the CONFIG register.
3. Write 1100 1000 1000 0000b = C880h to T_SET
4. When the part has finished its first A/D conver-
5. Read out the contents of the CONFIG register:
6.Write 0111 1111 1000 0000b = 7F80h to T_SET
7.When the part has finished its next A/D conver-
8.Read CONFIG again, to clear the interrupt re-
9.Based on the results of the test in step (4), do the
{END}
{START Polling-Based Test and Initialization Rou-
1. Temporarily disable the host’s interrupt input
Routine}
temperature interrupt handling routine. Redirect
interrupts from the part under test to a handler
for the interrupt that will be generated in steps
(4) and (7) of this routine.
(The assumption is made that the host is an I
or SMBus part, and therefore responds to an ac-
tive-low interrupt request.)
and T_HYST. This corresponds to -55.5°C.
sion, INT will be asserted.
a) If the part is an MIC184, the MSB will be set
b) If the part is a conventional LM75-type part,
and T_HYST. This corresponds to +127.5°C.
sion, INT will be asserted a second time.
quest from step (7). This will also clear STS, if
the part under test is an MIC184.
following within 50ms total:
a) Set the CONFIG register as required.
b) Load T_HYST with its operational value.
c) Load T_SET with its operational value.
d) Set the host’s interrupt handling routine back
tine}
to one (CONFIG = 1000 0010b = 82h).
the MSB will be zero (CONFIG = 0000
0010b = 02h).
to overtemperature and undertemperature
mode.
MIC184
2
C
Micrel