MTE1122/SO Microchip Technology, MTE1122/SO Datasheet - Page 2
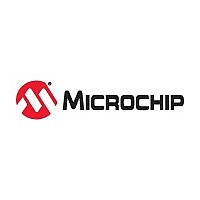
MTE1122/SO
Manufacturer Part Number
MTE1122/SO
Description
IC ENERGY CONTROLLER 18-SOIC
Manufacturer
Microchip Technology
Specifications of MTE1122/SO
Voltage - I/o High
0.7V
Voltage - I/o Low
0.6V
Current - Supply
1.8mA
Voltage - Supply
4 V ~ 6 V
Operating Temperature
0°C ~ 70°C
Mounting Type
Surface Mount
Package / Case
18-SOIC (0.300", 7.50mm Width)
Meter Type
Single Phase
Lead Free Status / RoHS Status
Request inventory verification / Request inventory verification
AN599
THEORY OF OPERATION
Power Consumption
In an induction motor, the current draw at no load is
quite high because the stator windings must supply all
the magnetic field energy. This means that, even when
idling, the motor draws a major portion of its full-load
current. The energy not converted into work is con-
verted into heat and vibration. In addition to being
wasted, the heat and vibration shortens the life of
lubricants, bearings, and other components in the
vicinity.
The torque produced by an AC motor is proportional to
the square of the applied voltage. Thus, a motor
producing part of its rated load only needs part of its
rated voltage.
Power Factor
In an induction motor, the current in the windings lags
the voltage, due to the inductive reactance in the
windings (Figure 10). The cosine of the amount of lag
in degrees is the power factor. Power factors are 1.0 for
resistive loads (heaters, etc.) and vary from close to 1
for a fully loaded motor, to as low as 0.1 for an idling
motor. The actual power being consumed by the motor
is:
A lightly loaded induction motor has low power factor.
As the motor reaches its rated load, its power factor
gets closer to 1. How close it gets to 1 will depend on
the motor’s internal design. Values around 0.65 are
typical of single-phase motors.
The MTE1122 calculates motor loading by measuring
the time between current and voltage zero-crossings,
in effect, power factor. When the load on the motor is
low, the power consumed by the motor can be lowered
by lowering the voltage applied to the motor, which is
done by turning a triac on at the proper time during the
voltage cycle. (Figure 10 for waveforms.) The resulting
voltage across the motor, and the zero-crossing times,
are monitored, and adjusted on a cycle-by-cycle basis,
as determined by the proprietary algorithms in the
MTE1122. At no load, the voltage to the motor can be
as low as 85 VAC, instead of the usual 120 VAC. Power
consumption can be cut by as much as 58%,
depending on load, and operating temperature lowered
by as much as 45 F. Refer to the system block diagram
in Figure 1, and the graph in Figure 2 and Table 1.
A motor powered by the MTE1122 and this energy
management control circuit will draw less current. Its
power factor will also be improved; however, the power
factor seen by the line will NOT be improved.
DS00599B-page 2
(Voltage) (Current) (Power Factor)
ENERGY MEASUREMENT
To measure the true power of an induction motor
requires the use of a true-RMS power meter, one that
will measure non-sinusoidal waveforms. Models of this
type of instrument are available from Fluke and
Tektronix, among others.
Measurements for this Application Note were made
using the following equipment:
Hampden Engineering Corp:
CSM-100 1/3 HP motor
DYN-100A Dynamometer
Rl-100A Load bank
HPT-100 Digital Photo Tachometer
Tektronix Corp:
THM560 Scopemeter
A622 Current probe
The voltage, current, and true-RMS power supplied to
the Energy Management Control System driving a
1/3 HP motor were measured with the meter and
current probe. The motor RPM was measured with the
photo-tach. The torque supplied by the motor was
measured with the dynamometer, which also supplied
the adjustable load on the motor.
Motor Power Out in Watts is calculated by:
Power Out in Horsepower is calculated by:
n is RPM
Efficiency, in percent (%), is calculated by:
is in Newton-meters
(Power Out)/(Power In) 100
P=( n)/7142.72
P= n)/5.18
1995 Microchip Technology Inc.