JFW100G Lineage Power, JFW100G Datasheet - Page 17
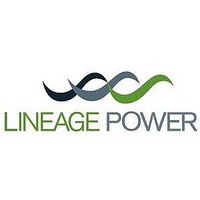
JFW100G
Manufacturer Part Number
JFW100G
Description
Manufacturer
Lineage Power
Datasheet
1.JFW100G.pdf
(24 pages)
April 2008
Thermal Considerations
Heat Transfer with Heat Sinks
Use Figure 25 to determine air velocity for the 1/2 inch
heat sink. The minimum airflow necessary for this mod-
ule is about 2.0 m/s (400 ft./min.).
Custom Heat Sinks
A more detailed model can be used to determine the
required thermal resistance of a heat sink to provide
necessary cooling. The total module resistance can be
separated into a resistance from case-to-sink (θcs) and
sink-to-ambient (θsa) shown below (Figure 26).
Figure 26. Resistance from Case-to-Sink and
Lineage Power
P
D
Sink-to-Ambient
∅
T
C
θcs
dc-dc Converters; 36 to 75 Vdc Input; 2.5 Vdc Output; 25 W to 75 W
T
S
(continued)
θsa
(continued)
T
A
8-1304 (C)
For a managed interface using thermal grease or foils,
a value of θcs = 0.1 °C/W to 0.3 °C/W is typical. The
solution for heat sink resistance is:
This equation assumes that all dissipated power must
be shed by the heat sink. Depending on the user-
defined application environment, a more accurate
model, including heat transfer from the sides and bot-
tom of the module, can be used. This equation pro-
vides a conservative estimate for such instances.
EMC Considerations
For assistance with designing for EMC compliance,
please refer to the FLTR100V10 data sheet
(DS99-294EPS).
Layout Considerations
Copper paths must not be routed beneath the power
module mounting inserts. For additional layout guide-
lines, refer to the FLTR100V10 data sheet
(DS99-294EPS).
θsa
=
(
----------------------- -
T
C
P
–
D
T
A
)
–
θcs
17