JW100M1 Lineage Power, JW100M1 Datasheet - Page 6
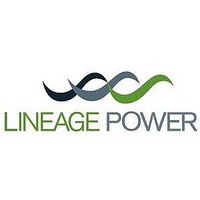
JW100M1
Manufacturer Part Number
JW100M1
Description
Manufacturer
Lineage Power
Datasheet
1.JW100M1.pdf
(16 pages)
dc-dc Converters; 36 to 75 Vdc Input, 1.5 Vdc Output; 15 W to 45 W
Test Configurations
Note: Measure input reflected-ripple current with a simulated source
Note: Use a 1.0 µF ceramic capacitor and a 10 µF aluminum or
Figure 6. Peak-to-Peak Output Noise Measurement
Note: All measurements are taken at the module terminals. When
Figure 7. Output Voltage and Efficiency
6 6
BAT T ER Y
Figure 5. Input Reflected-Ripple Test Setup
η
inductance (L
tery impedance. Measure current as shown above.
tantalum capacitor. Scope measurement should be made
using a BNC socket. Position the load between
51 mm and 76 mm (2 in. and 3 in.) from the module.
socketing, place Kelvin connections at module terminals to
avoid measurement errors due to socket contact resistance.
=
T O OSC ILLOSC OPE
⎛
⎝
SUPPLY
[
----------------------------------------------- -
Test Setup
Measurement Test Setup
V
V
RESISTANCE
V
[
CONTACT
O
O
V
O
(+)
(–)
I
(+) – V
(+) – V
TEST
I
I
C
ESR < 0.1 •
@ 20 °C , 100 kH z
) of 12 µH. Capacitor C
S
COPPER STRIP
O
220 µ F
1.0 µF
I
(–)
(–)
12 µ H
V
V
I
I
L
(+)
(–)
T E S T
]I
]I
I
O
SENSE(+)
SENSE(–)
⎞ x 100
⎠
10 µF
V
V
O
O
ESR < 0.7 •
@ 100 kH z
(+)
(–)
33 µ F
C U R R EN T
PR OBE
SCOPE
DISTRIBUTION LOSSES
S
I
O
offsets possible bat-
CONTACT AND
%
RESISTIVE
LOAD
LOAD
V
V
8-513 (C).d
I
8-203 (C).l
I
( + )
( –)
8-749 (C)
Design Considerations
Input Source Impedance
The power module should be connected to a low
ac-impedance input source. Highly inductive source
impedances can affect the stability of the power mod-
ule. For the test configuration in Figure 5, a 33 µF elec-
trolytic capacitor (ESR < 0.7 ¾ at 100 kHz) mounted
close to the power module helps ensure stability of the
unit. For other highly inductive source impedances,
consult the factory for further application guidelines.
Safety Considerations
For safety-agency approval of the system in which the
power module is used, the power module must be
installed in compliance with the spacing and separation
requirements of the end-use safety agency standard,
i.e., UL1950, CSA C22.2 No. 950-95, and VDE 0805
(EN60950, IEC950).
If the input source is non-SELV (ELV or a hazardous
voltage greater than 60 Vdc and less than or equal to
75 Vdc), for the module’s output to be considered
meeting the requirements of safety extra-low voltage
(SELV), all of the following must be true:
n
n
n
n
Note: Do not ground either of the input pins of the
The power module has extra-low voltage (ELV) outputs
when all inputs are ELV.
The input to these units is to be provided with a maxi-
mum 20 A normal-blow fuse in the ungrounded lead.
The input source is to be provided with reinforced
insulation from any hazardous voltages, including the
ac mains.
One V
both the input and output pins are to be kept floating.
The input pins of the module are not operator acces-
sible.
Another SELV reliability test is conducted on the
whole system, as required by the safety agencies, on
the combination of supply source and the subject
module to verify that under a single fault, hazardous
voltages do not appear at the module’s output.
module without grounding one of the output pins.
This may allow a non-SELV voltage to appear
between the output pin and ground.
I
pin and one V
O
pin are to be grounded or
Lineage Power
April 2008