NJM#3717FM2 NJR, NJM#3717FM2 Datasheet - Page 9
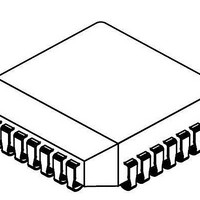
NJM#3717FM2
Manufacturer Part Number
NJM#3717FM2
Description
Motor / Motion / Ignition Controllers & Drivers Stepper
Manufacturer
NJR
Type
Stepper Motor Controllerr
Datasheet
1.NJM3717D2.pdf
(10 pages)
Specifications of NJM#3717FM2
Product
Stepper Motor Controllers / Drivers
Operating Supply Voltage
5 V
Supply Current
25 mA
Mounting Style
SMD/SMT
Package / Case
PLCC-28
Lead Free Status / Rohs Status
Lead free / RoHS Compliant
Available stocks
Company
Part Number
Manufacturer
Quantity
Price
Analog control
As the current levels can be continuously controlled by modulating the V
achieved.
Switching frequency
The motor inductance, together with the pulse time, t
The choice of motor may then require other values on the R
to obtain a switching frequency above the audible range. Switching frequencies above 40 kHz are not recom-
mended because the current regulation can be affected.
Sensor resistor
The R
choice for 415 mA max motor current at V
The peak motor current, im , can be calculated by using the formulas:
i
i
i
Heatsinking
The junction temperature of the chip highly effects the lifetime of the circuit. In high-current applications, the
heatsinking must be carefully considered.
printed circuit board (see figure 10) or by applying an external heatsink type V7 or V8, see figure 9.
board copper must be connected to electrical ground.
forced-air cooling may be available to reduce the temperature rise of the circuit.
m
m
m
C, for heatsinks of the type V7, V8 or a 20 cm
The Rth
The diagram in figure 16 shows the maximum permissible power dissipation versus the ambient temperature in
For motor currents higher than 500 mA, heatsinking is recommended to assure optimal reliability.
The diagrams in figures 9 and 10 can be used to determine the required heatsink of the circuit. In some systems,
= (V
= (V
= (V
S
R
R
R
resistor should be of a non-inductive type, power resistor. A 1.0 ohm resistor, tolerance
• 0.083) / R
• 0.050) / R
• 0.016) / R
j-a
of the NJM3717 can be reduced by soldering the ground pins to a suitable copper ground plane on the
Figure 9. Heatsinks, Staver, type V7 and V8 by Columbia-Staver UK
S
S
S
Figure 10. Copper foil used as a heatsink
[A], at 100% level
[A], at 60% level
[A], at 20% level
90
80
70
60
50
40
30
Thermal resistance [ C/W]
PCB copper foil area [cm ]
5
PLCC package
DIP and EMP package
10
15
R
= 5V.
20
2
copper area respectively. Any external heatsink or printed circuit
25
2
30
off
, determines the switching frequency of the current regulator.
35
T
, C
T
components than those recommended in figure7,
R
28-pin
input, limited microstepping can be
16-pin
PLCC
20-pin
EMP
DIP
NJM3717
1%, is a good