ADXL150AQC Analog Devices Inc, ADXL150AQC Datasheet - Page 7
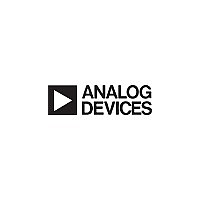
ADXL150AQC
Manufacturer Part Number
ADXL150AQC
Description
IC ACCELEROMETER LP SGL 14CERPAK
Manufacturer
Analog Devices Inc
Series
iMEMS®r
Datasheet
1.ADXL150EM-1.pdf
(15 pages)
Specifications of ADXL150AQC
Rohs Status
RoHS non-compliant
Axis
X or Y
Acceleration Range
±50g
Sensitivity
38mV/g
Voltage - Supply
4 V ~ 6 V
Output Type
Analog
Bandwidth
1kHz
Mounting Type
Surface Mount
Package / Case
14-CerPak
Interface
-
Available stocks
Company
Part Number
Manufacturer
Quantity
Price
Part Number:
ADXL150AQC
Manufacturer:
ADI/亚德诺
Quantity:
20 000
REV. 0
THEORY OF OPERATION
The ADXL150 and ADXL250 are fabricated using a propri-
etary surface micromachining process that has been in high
volume production since 1993. The fabrication technique uses
standard integrated circuit manufacturing methods enabling all
the signal processing circuitry to be combined on the same chip
with the sensor.
The surface micromachined sensor element is made by deposit-
ing polysilicon on a sacrificial oxide layer that is then etched
away leaving the suspended sensor element. Figure 14 is a
simplified view of the sensor structure. The actual sensor has
42 unit cells for sensing acceleration. The differential capacitor
sensor is composed of fixed plates and moving plates attached to
the beam that moves in response to acceleration. Movement of
the beam changes the differential capacitance, which is measured
by the on chip circuitry.
The sensor has 12-unit capacitance cells for electrostatically
forcing the beam during a self-test. Self-test is activated by the
user with a logic high on the self-test input pin. During a logic
high, an electrostatic force acts on the beam equivalent to
approximately 20% of full-scale acceleration input, and thus a
proportional voltage change appears on the output pin. When
activated, the self-test feature exercises both the entire mechani-
cal structure and the electrical circuitry.
All the circuitry needed to drive the sensor and convert the
capacitance change to voltage is incorporated on the chip requiring
no external components except for standard power supply decou-
pling. Both sensitivity and the zero-g value are ratiometric to
the supply voltage, so that ratiometeric devices following the
accelerometer (such as an ADC, etc.) will track the accelerom-
eter if the supply voltage changes. The output voltage (V
a function of both the acceleration input (a) and the power
supply voltage (V
Both the ADXL150 and ADXL250 have a 2-pole Bessel switched-
capacitor filter. Bessel filters, sometimes called linear phase
filters, have a step response with minimal overshoot and a maxi-
mally flat group delay. The –3 dB frequency of the poles is
preset at the factory to 1 kHz. These filters are also completely
self-contained and buffered, requiring no external components.
Figure 14. Simplified View of Sensor Under Acceleration
PLATE
CAPACITANCES
V
OUT
S
FIXED
PLATE
) as follows:
= V
ANCHOR
S
/2 – (Sensitivity
UNIT CELL
BEAM
V
5V
S
a)
OUT
) is
–7–
MEASURING ACCELERATIONS LESS THAN 50 g
The ADXL150/ADXL250 require only a power supply bypass
capacitor to measure 50 g accelerations. For measuring 50 g
accelerations, the accelerometer may be directly connected to an
ADC (see Figure 25). The device may also be easily modified to
measure lower g signals by increasing its output scale factor.
The scale factor of an accelerometer specifies the voltage change
of the output per g of applied acceleration. This should not be
confused with its resolution. The resolution of the device is the
lowest g level the accelerometer is capable of measuring. Resolu-
tion is principally determined by the device noise and the mea-
surement bandwidth.
The zero g bias level is simply the dc output level of the accelerom-
eter when it is not in motion or being acted upon by the earth’s
gravity.
Pin Programmable Scale Factor Option
In its normal state, the ADXL150/ADXL250’s buffer amplifier
provides an output scale factor of 38 mV/g, which is set by an
internal voltage divider. This gives a full-scale range of 50 g
and a nominal bandwidth of 1 kHz.
A factor-of-two increase in sensitivity can be obtained by con-
necting the V
not needed for offset adjustment. This connection has the effect
of reducing the internal feedback by a factor of two, doubling
the buffer’s gain. This increases the output scale factor to 76 mV/g
and provides a 25 g full-scale range.
Simultaneously, connecting these two pins also increases the
amount of internal post filtering, reducing the noise floor and
changing the nominal 3 dB bandwidth of the ADXL150/
ADXL250 to 500 Hz. Note that the post filter’s “Q” will also
be reduced by a factor of 2 from 0.58 (Bessel response) to a
much gentler “Q” value of 0.41. The primary effect of this
change in “Q” is only at frequencies within two octaves of the
corner frequency; above this the two filter slopes are essentially
the same. In applications where a flat response up to 500 Hz is
needed, it is better to operate the device at 38 mV/g and use an
external post filter. Note also that connecting V
pin adds a 30 k load from V
at V
ADXL250’s 100 A (typical) output current drive.
OUT
, this added load will consume 60 A of the ADXL150/
OUT
pin to the offset null pin, assuming that it is
OUT
ADXL150/ADXL250
to V
S
/2. When swinging 2 V
OUT
to the offset